Everything you need to
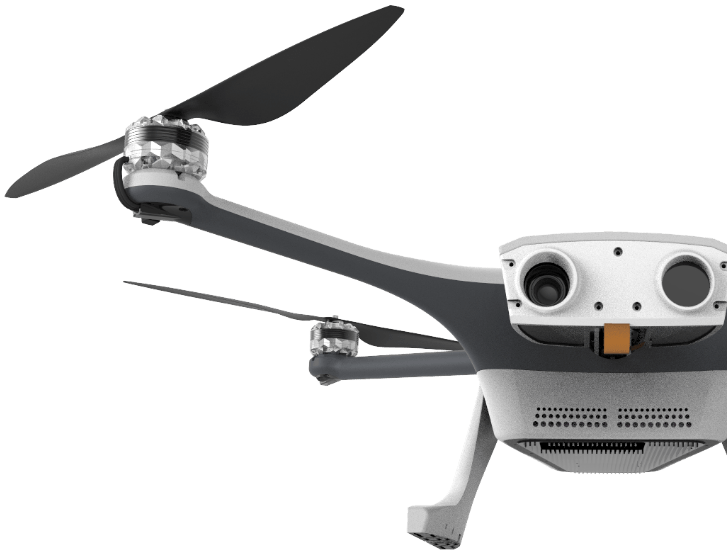
While companies are already successfully using drones and autonomous robots to collect data, they are missing the ability to both gather and analyze visual data efficiently using one system. This is where Autonomous Inspection and Monitoring (AIM) comes in. It’s a completely new concept, providing a revolutionary end-to-end solution that fully automates the entire site inspection process.
AIM is the future of site inspections and the future is coming faster than you think. This guide will tell you everything you need to know about this exciting new field, including:
- How are sites inspected today?
- How is the industry moving towards fully autonomous inspections?
- What does an autonomous inspection look like?
- What are the main advantages of autonomous site inspections?
- What industries can benefit most from autonomous site inspection and monitoring?
- What companies have already implemented autonomous inspection solutions?
Why is optimizing site
inspections important?
Site inspections are a crucial part of the regular operations of any industrial site. They are conducted to ensure that the vital infrastructure and assets are up-and-running and operating at maximum efficiency. The goal of most regular inspections is to prevent downtime, failures and safety risks.
Site inspections are also used to track progress of sites under construction, to measure materials and supplies and, of course, to track working conditions and flag any potential safety risks to employees.
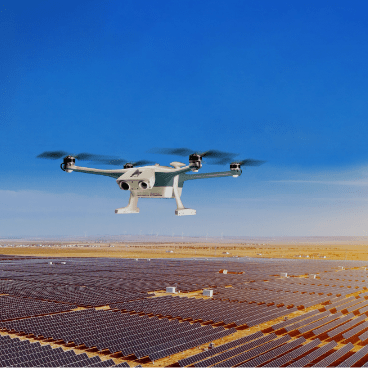
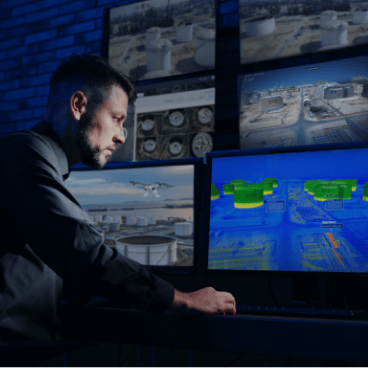
Following a site inspection, managers and other relevant employees receive reports indicating areas that need to be addressed or fixed. This information is used to make business decisions and to determine where to direct attention and resources.
As we will describe in greater detail below, the way site inspections are currently conducted relies heavily on manpower which leaves them open to human error and inefficiencies.
How are industrial sites inspected today?
Facilities today are typically inspected manually, although some facilities have started to turn to piloted drones and robots to take over certain elements of inspections. Site inspections involve multiple steps, each one requiring significant investment of human time and effort. Traditional inspections begin with a physical tour of the facility during which the inspector visually examines the site and relevant assets, takes measurements, collects information from IoT sensors where they exist, and takes several photographs. Even if this step is assisted by drones or visual inspection software, personnel is typically needed to pilot the drones or manage the software.
Once all of this information is collected, it needs to be uploaded to various databases or systems. From there, it is analyzed by subject matter experts or data analysts who must sort through hundreds of gigabytes of information to find what is relevant for their reports. Some companies use data interpretation solutions to make this process shorter, but even so, significant human intervention is required. Once the data is finally analyzed, it is put into reports and delivered to key stakeholders who use the information to make decisions.
If you are tired just reading that, imagine what it’s like for the people actually doing all that manual labor!
This process, which relies so heavily on human input, is fraught with challenges, including:
Frequency
Most site inspections are only done once or twice a year because of the high costs involved (both in terms of money and time). Such infrequent inspections leave a lot of room for error or missed risks.
Quality
Manual inspections are subject to human error. The inspector has to be sure to use the right type of equipment and catch the exact right angle with the perfect lighting in order to get an accurate picture of what is happening at a facility.
Consistency
Because inspections are done infrequently and often by different inspectors (or the same inspector who takes photographs at different angles each time), it is difficult to monitor changes over time and therefore flaws and damages can easily be missed.
Lack of access to data
Once the data is collected, it has to be uploaded for analysis. Again, as a manual process this is not necessarily done systematically or efficiently and data can end up being uploaded to the wrong place or tagged incorrectly. This increases the likelihood of data analysts missing important information.
What does an autonomous inspection look like?
An autonomous inspection can be as easy as ordering something online! You simply place your order for the specific insights that you need and then sit back and wait for the results to arrive in your inbox. Here’s a breakdown of what happens:
01. Order insight
A request for information about a specific asset or area is submitted to the system.
02. Capture
A robot is dispatched autonomously and collects the relevant data.
03. Upload
The visual data that was collected is automatically uploaded to the cloud.
04. Analysis
The data is sorted and analyzed against past data.
05. Report
Insights and any relevant data assets such as 3D models or anomalies are automatically compiled into a report.
06. Insight delivery
The report is delivered to the relevant stakeholders.
This new method of making site inspections completely autonomous is transforming the way data is collected and perceived in the following key ways:
Data democratization
A cloud-based system democratizes visual data giving anyone in the company access to the specific information they need.
Automated data collection
Aerial, ground and sea robots can be automatically dispatched to monitor sites and collect data continuously and consistently catching the same angle and lighting to enable direct comparisons.
Unify visual data
Visual data collected by any device (from a basic camera to a high-tech drone) can be stored, managed and analyzed in one location.
Automate insights
Schedule AI-driven reports on anomalies, trends, 3D models, measurements and anything else you might want to know.
Remote operations
The entire inspection and monitoring process can be done remotely, from the safety and comfort of an employee’s home or office.
Autonomous inspection and monitoring (AIM) at work
Mike Kleis, Vice President of Operations and Plant Manager at Koch Fertilizer’s production facility in Enid, Oklahoma incorporated autonomous site inspections into the plant’s operations. His goal was to alleviate the monotonous, difficult and sometimes dangerous tasks that employees would have to do by automating them. According to Mike,
Safety and maintenance tasks can sometimes comprise an employee’s entire shift. Autonomous drones can do the same inspection work in minutes – without scaling a 190-foot tower or walking miles of railway inspecting rail cars for leaks. This allows more time for individuals to focus on more fulfilling work.
Partially automated inspection systems can do some of what’s described above, but only a fully autonomous inspection and monitoring solution will provide all of these benefits. Percepto AIM is the first end-to-end solution that brings together the entire process – from data capture to actionable insights.
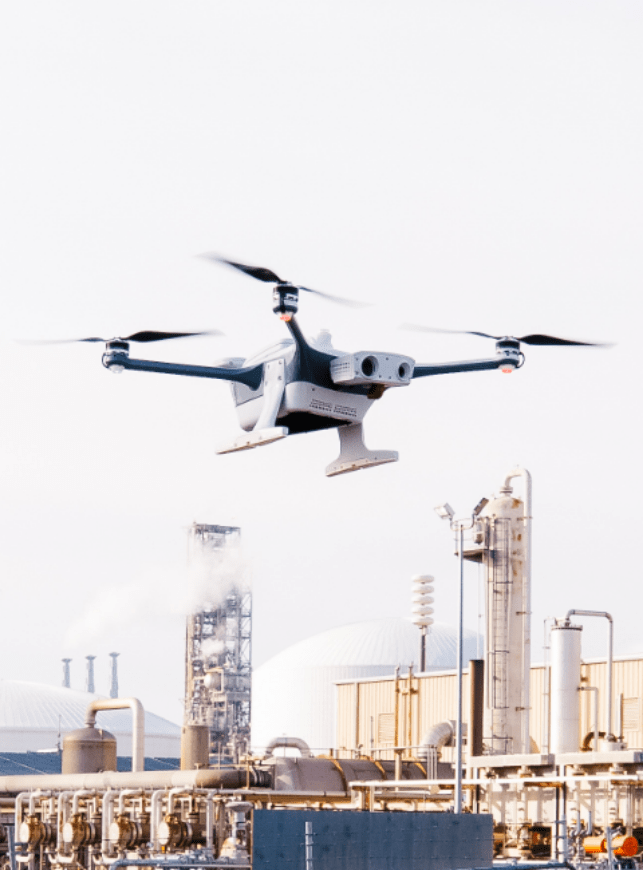
How is the industry moving towards fully autonomous inspections?
Let’s get some key terminology straight because it can be confusing. Currently, most inspections are done manually, as described above. The industry is moving towards fully autonomous inspection and monitoring, but we can look at autonomy as a spectrum with multiple stages along the way between manual inspections and fully autonomous ones.
When it comes to fully automating inspections, there are two distinct parts of the process, each of which can be automated in its own way: visual data collection and visual data management.
What is autonomous visual data collection?
While there are several robots on the market today that claim to be fully autonomous, they require people to help them navigate, collect data and return to their charging station. Because of the requirement of a human to be involved, this type of robot could be described as highly automated, but not quite autonomous.
- Manual data collection
- Piloted drones and robots
- Pilot assisted drones and robots
- Remotely operated drones and robots
- Site perception
Manual data collection
An employee manually inspects the facility using cameras.
Piloted drones and robots
An employee or service provider uses piloted drones or robots to manually inspect the facility.
Pilot assisted drones and robots
Self-navigating, highly automated drones and robots navigate the facility with the help of an on-site pilot.
Remotely operated drones and robots
On-site smart housing enables a fully autonomous inspection cycle without an on-site pilot.
Site Perception (self learning site inspection solution a.k.a fully autonomous)
Autonomous drones and robots learn the facility as they operate, determining which assets to inspect, when to inspect them and what data to capture.
To fully automate the data collection process, an autonomous robot (i.e. not requiring any human intervention at all) has to be able to go out into the field and collect data using computer vision and AI. As described in Stage 5 above, in a fully autonomous system, the drones and robots themselves use AI to learn all of the ins and outs of the facility they inspect. They can then decide when it’s necessary to inspect particular assets and what type of data is needed based on triggering events.
What is autonomous visual data management?
Of course, data collection is only half the story. For a complete solution, once the data is collected, the management and analysis must also be autonomous. Most visual data management solutions don’t automatically upload the collected data to the cloud, and an employee is required to physically upload data to a 3rd party system to be analyzed. This automatic upload is a key feature of a fully autonomous solution, which also tags, sorts, and analyzes data automatically and then generates reports.
Autonomous inspection and monitoring (AIM) at work
The technology is a game-changer.
So says Florida Power & Light CEO, Eric Silagy. FPL uses Percepto’s drone-in-a-box equipped with a thermal camera to help them identify issues before they cause a power outage. The company has also begun a pilot program using Boston Dynamics’ Spot®, a robodog which uses a thermal camera and a high resolution camera. Integrated with Percepto AIM, Spot can safely get to hard-to-access areas that even rugged land rovers can’t get to, providing critical information to site employees.

What are the elements of an autonomous site inspection system?
A fully autonomous inspection and monitoring system consists of 2 parts – a visual data collection platform and visual data management software.
Data collection platform: drones and robots
Instead of a site employee manually inspecting industrial sites, in an automated inspection, autonomous robots collect the data. Drones or other autonomous robots navigate around the site equipped with cameras and other data collection tools that enable them to capture relevant information.
Again, it’s important to distinguish between robots that claim to be autonomous and a fully autonomous one. A truly fully autonomous robot, for example, is able to monitor its own battery level and return to the charging station when necessary in order to be ready for the next mission. This eliminates the need for a person to go out into the field, collect the robot and dispatch it on its next mission. Fully autonomous robots are able to replicate tasks that an employee could do with no human intervention at all. That means, they offer:
Remote site monitoring
The robots are always on site even when no humans are there, available to run inspections and provide situational awareness.
Safer inspections
Robots perform inspections at high altitudes and in inclement weather, collecting data without putting employees at risk.
Better data and better insights
Robots always collect consistent and high-quality data, crucial for generating actionable insights.
24/7 availability
Robots are stationed on-site in weatherproof smart houses, ready to collect data at a moment’s notice.
Percepto autonomous robots are integrated with AIM and therefore have the ability to conduct multiple missions over time with no human intervention, delivering key insights to site managers and stakeholders. Our drone-in-a-box solutions, Percepto Air, are the best examples of an autonomous robot, as our engineers specifically designed them to operate without human intervention – from a ruggedized Percepto Base to safety routines and of course PerceptoCore AI algorithms. Percepto can integrate any robot into its ecosystem, similar to Boston Dynamics’ Spot, which now has a Percepto Base for Spot, Percepto payload and is integrated into AIM.
Visual data management solution
In an autonomous system, the data collection is a means to an end, with the ultimate goal being relevant and actionable data presented to the right people. This means that the data collection system must automatically connect to the data analysis system so that relevant data is constantly being collected and then translated into actionable reports in real time. Most systems today can analyze data on an ad-hoc basis, but cannot necessarily pinpoint the specific analytics to run on certain data in order to get the desired insight. An autonomous inspection and monitoring platform like Percepto’s AIM, in comparison, works in the following way:
- Autonomous robots monitor site assets and infrastructure, with real-time alerts for critical issues sent to relevant stakeholders.
- Data captured is automatically uploaded to the cloud, where it’s tagged and stored for analysis.
- Analysis is conducted automatically using both ongoing and historical data in order to accurately detect anomalies and identify trends based on high resolution maps, temperature maps, 3D maps, volumetric measurements and more.
- Insights are delivered in order to focus stakeholder attention on the most urgent matters.
Because the AIM platform conducts remote inspections continuously, the software “learns” the assets and can easily detect changes over time and then report on them.
The key to a fully autonomous inspection and monitoring system is the integration of the automated inspection process and the automatic data analysis. With a fully autonomous inspection system, the right information gets into the hands of the right people quickly.
Autonomous inspection and monitoring (AIM) at work
Michael Dorr manages Florida Power & Light’s drone operations and is responsible for monitoring and inspecting all assets, especially after a hurricane. By using Percepto’s system, Michael can schedule drone flights over impacted assets either during or after the storm to assess the damage all from the safety of his own office. Drones that know when their batteries are running low and return to the charging station of their own accord means no risk of mid-mission failures. According to Michael,
this is a huge upgrade compared to how the company used to run inspections after a storm with cumbersome piloted drones.
Flights can take place every day and use image recognition to identify a potential issue and reduce the number of outages to the customers all while protecting the safety of the crews.
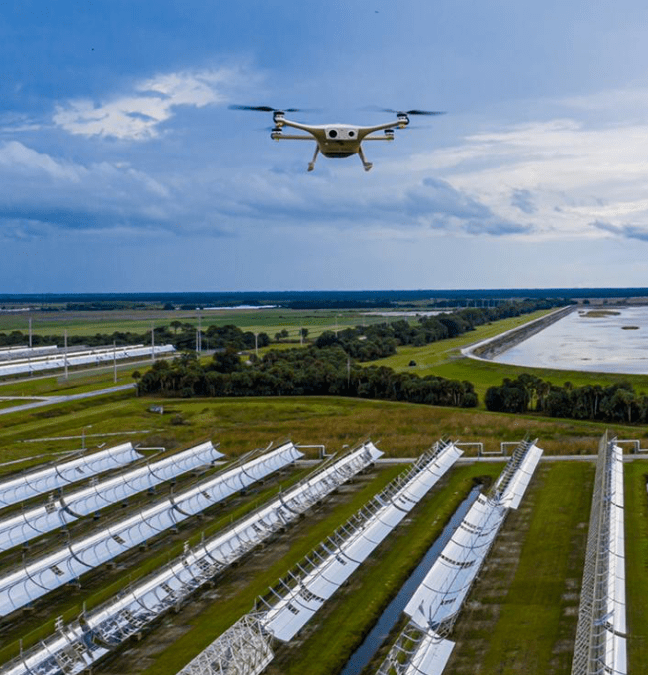
What is an autonomous site inspection used for?
Basically, any site inspection or monitoring of industrial sites that is typically done manually can be safer and better when conducted autonomously. Here are a few applications of autonomous inspection and monitoring:
- Inspection rounds
- Modeling and measurement
- Work progress monitoring
- Security
- Emergency response
- Remote operations
Inspection rounds
An autonomous robot can do the standard inspection rounds otherwise done by an employee, but more often and with more consistent high quality data-collection, boosting site productivity and freeing up employee time.
Read more
Modeling and measurement
Autonomous drones and robots can create 3D models of sites. At mining facilities, for example, volumetric measurements can be automatically generated, aiding logistics and operations teams.
Read more
Work progress monitoring
Construction projects are notorious for delays that can have major financial implications for a company. Autonomous site inspections allow for ongoing monitoring of the situation that can alleviate some of the factors that may lead to delay, such as ensuring that the right number of workers are there, monitoring usage of raw materials, and preventing theft or fraud.
Read more
Security
Any site is at risk for potential break-ins or vandalism especially if they are left unmanned for any period of time. Autonomous security patrols can alert management to intruders or other security risks in real time so the threat can be addressed before any damage is done.
Read more
Emergency response
When emergency strikes, it is critical for sites to respond quickly and safely to minimize damage and downtime. Autonomous robots can enable rapid response by providing instant visual data of a situation as it unfolds.
Read more
Remote operations
Managers can monitor assets such as electricity grids, pipelines, insulation and other specific types of equipment including tanks and stacks located in multiple geographic areas. Continuous remote inspection means early identification of faults before they escalate and lead to a major breakdown and loss of productivity.
Read more
Autonomous inspection and monitoring (AIM) at work
Sometimes it’s just too dangerous to send employees out to a site even when the operations of that site are critical. In September, 2020 a massive wildfire broke out in Big Hollow, Washington. Verizon’s infrastructure was in danger of being damaged which would knock out critical communication abilities for first responders. The company was granted a special waiver by the FAA to be allowed to fly Percepto’s Sparrow drone remotely in order to inspect their infrastructure. According to Rima Qureshi, Verizon’s Chief Strategy Officer,
innovations in airborne technology have enhanced our ability to inspect our sites without putting engineers in harm’s way, and provide our first responders with reliable communications.
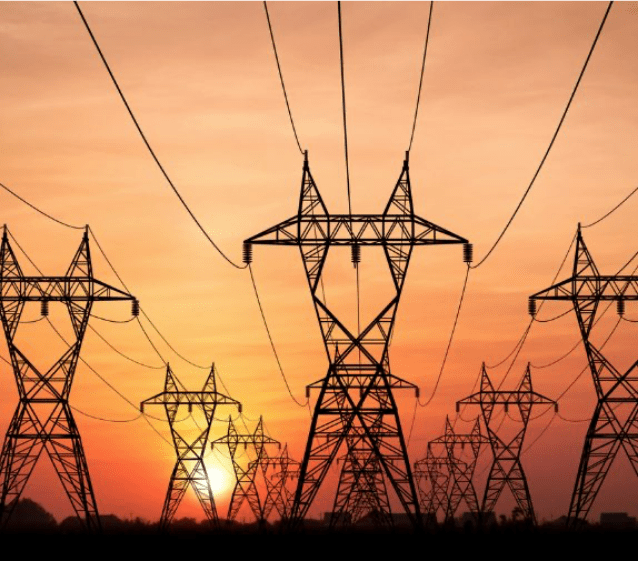
What are the main advantages of autonomous site inspections?
The advantages are many, but let’s go through the top benefits here:
Remote operations
If the Covid-19 pandemic has taught us anything, it’s that remote work is possible and sometimes preferable. When it comes to site inspections, it’s almost always preferable to work remotely to avoid sending inspectors into dangerous situations, inclement weather and hard to reach places. It’s not just about safety, remote inspections also significantly impact industrial companies’ bottom line. Cost savings are realized through the ability to inspect and monitor several sites from one central location and by eliminating the need to pay for the hours of time an inspector would need to spend.
Reduction in downtime
When assets or infrastructure have planned or unplanned downtime, it costs companies hundreds of billions of dollars per year. For certain industries, like utilities or telecommunications, it also damages their reputation when customers are left in the lurch without electricity or phones. Autonomous monitoring means continuous visual inspection of all assets and key infrastructure and real time analysis that flags any potential issues. Early detection of problems is key to supporting preventive maintenance strategies allowing issues to be addressed and fixed before causing downtime.
Employee safety
In-person site inspections require employees to take personal safety risks. Whether it is climbing high towers or dangerous tanks filled with chemicals, there is always the possibility of injury. In fact, 80-90% of accidents at industrial sites are caused by human error. When robots do the job, the risk of human error is all but eliminated. Robots and drones can also respond fast to an emergency such as a fire or an explosion at a refinery, without putting any human employees in danger.
Minimized environmental impact
Heavy industrial sites such as refineries, mines and power plants are all at risk for leaks, spills or other disasters that could have significant environmental repercussions, incurring serious fines and damaging a company’s reputation. Continuous monitoring by autonomous drones or other robots can minimize risks and prevent such a disaster from occurring. In addition, industrial corporations of all kinds are often blamed for environmental damages. While sometimes they truly are to blame, there are times that false accusations are made despite the fact that the companies have adhered to all of the required regulations. Drones that monitor daily operations for leaks or high temperatures can help minimize pollution and help industrial sites adhere to regulatory compliance.
Reduced operational costs and increased productivity
Investing in an autonomous and remote inspection and monitoring system is a cost effective way to ensure that all assets and key infrastructure are up and running at maximum efficiency at all times. This is great for a company’s bottom line, saving money on costly failures and lost revenue due to downtime and increasing profits by operating at peak efficiency.
Regulatory compliance
Frequent, consistent inspections will give companies a repository of data and information that can be used to prove compliance with regulations – should they be accused of improper behavior – and prevent being charged large fines. Continuous monitoring can also flag issues that are at risk of becoming compliance violations. For example, if a company must keep water temperatures below 35 degrees, they can receive an automatic alert when the temperature reaches 34.5 degrees.
Rapid response
In case of an emergency, autonomous robots can be ready to go in minutes. They can quickly access equipment in remote locations or that has been impacted by a fire or inclement weather making it unsafe or impossible for personnel to get there safely. This is crucial to provide situational awareness to emergency response teams, and to contain any emergency as quickly as possible.
Bolstered security
Industrial sites are at risk for security breaches, as critical infrastructure and raw materials are often targets for theft or attacks. Autonomous drones or robots can regularly patrol a facility checking for any intruders or vandalism. If suspicious activity is detected, the site managers can be alerted immediately so that they can take action.
What industries can benefit most from autonomous site inspection and monitoring?
In broad terms, any industry or company that has facilities or sites that require regular inspections could hugely benefit from switching to an autonomous system. Let’s discuss some of the most salient examples:
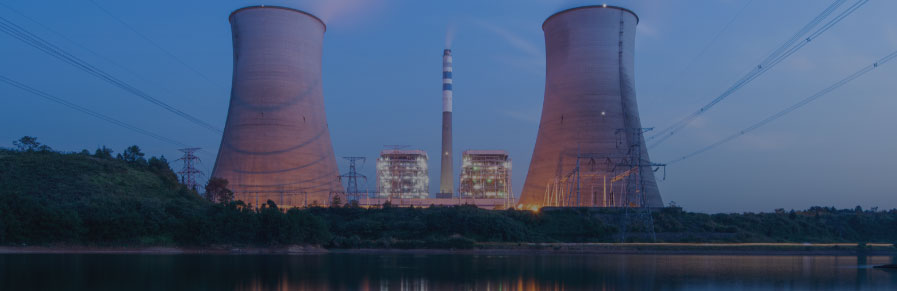
Energy, thermal power and utilities
The top priority for any energy company is boosting productivity and ensuring that reliable service is provided to its clients. For example at FPL, ensuring that its 9 million customers have reliable electricity is critical to the company’s solvency. The best way to ensure high productivity and reliable service is through regular site inspections to ensure that everything is running properly and to prevent catastrophic accidents that could have huge social and environmental impacts. .
Here’s what autonomous site inspections mean for energy, thermal power and utilities:
- Frequent high-quality inspections enable managers to make smart decisions based on data to boost productivity and efficiency.
- Visual, thermal and radiometric inspection capabilities make it easy to optimize maintenance.
- Consistent temperature monitoring ensures adherence to strict environmental regulations.
- Immediate alerts to safety hazards minimize safety risks.
- Faster and better responses to both routine and emergency needs.
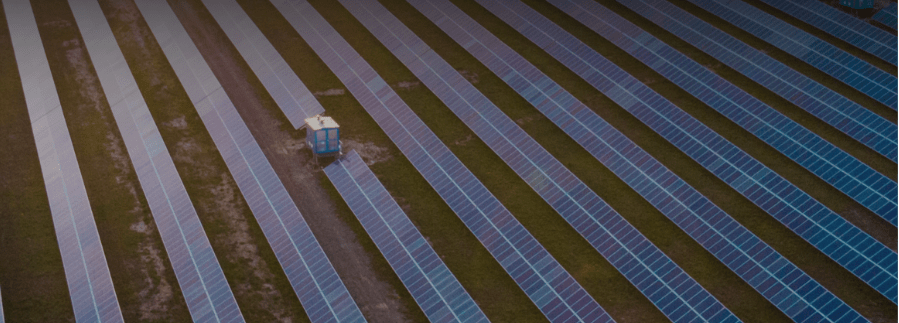
Renewables and solar energy
Solar energy companies need to have the ability to monitor both construction sites and daily operations remotely. Most solar sites are in far off locations that are hard to access, making remote operations a must in order to efficiently prevent breakdowns and productivity loss. Enel Green Power, for example, uses Percepto’s Sparrow drone to monitor their largest solar park in Spain. The drone can assess heat preservation and loss and detect temperature changes while workers remain at a safe distance.
Here’s what autonomous site inspections mean for the solar industry:
- Continuous monitoring ensures safe, continuous and efficient solar farm construction.
- Regular inspections mitigate risks of undetected faulty infrastructure and ensure that warranties are enforced.
- Consistent temperature monitoring ensures adherence to strict environmental regulations.
- Automatic security patrols and alerts offer augmented site security and safety
- Customized reports accessible to all stakeholders.
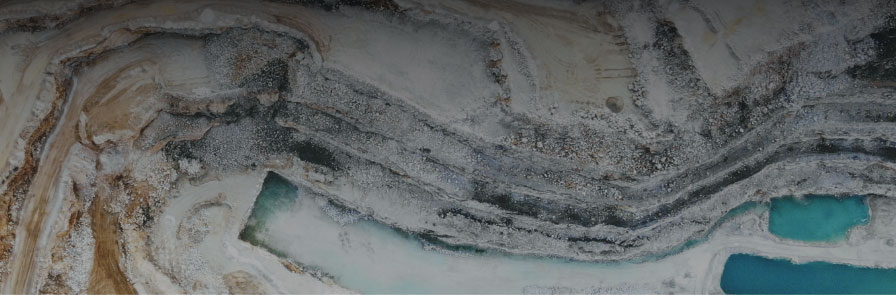
Mining
In the mining industry, safety is often the number one priority. Frequent inspections of remote assets are needed to ensure operational efficiency, yet often it isn’t safe to send an employee in to monitor the facility. For this reason, one of the largest mining conglomerates uses Percepto’s autonomous drones to remotely and continuously monitor their conveyor belts, trucks and other equipment at multiple sites, automatically detecting issues and reporting findings to the operations center. This close and constant monitoring has enabled them to achieve better site safety across their locations.
At a mine, autonomous site inspections mean:
- Safely monitor site operations without risking employees.
- Accurate 3D models for up-to-date inventory management.
- Easily confirm clearance of roadways and safety zones in advance of planned explosions.
- Routine perimeter patrols ensure site security.
- Immediate situational awareness in the event of an explosion or fire ensures a quicker and safer response.
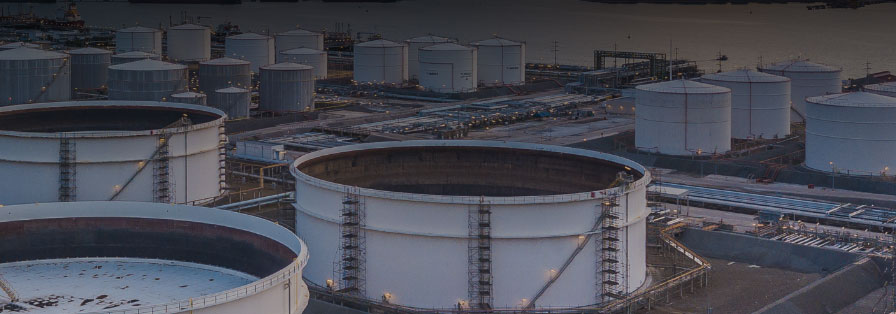
Oil and gas refineries
To reduce downtime without compromising on safety or compliance, oil and gas companies need accurate and real time visibility of all of their assets and infrastructure. Delek US gets this real time visibility by using Percepto’s solution which means that employees no longer have to climb high towers or go inside vessels in order to get the necessary data.
Here’s what autonomous site inspections mean for the oil and gas industry:
- Routine autonomous inspections can be scheduled to detect leaks and other flaws in hard-to-access or vulnerable locations.
- Thermal mapping monitors sensitive equipment for safety and production risks.
- Immediate situational awareness in the event of an explosion or fire ensures a quicker and safer response.
- Consistent monitoring and archiving of site conditions will ensure and prove compliance with all regulations.
- Routine perimeter patrols ensure site security.

Telecommunications
Telecom site monitoring ensures that infrastructure and installations are in good condition and can provide uninterrupted service to customers. Inspections of industrial telecommunications sites used to require that technicians climb to the top of towers to inspect the equipment. Now, companies can use autonomous inspection systems like Verizon did during a giant wildfire in Washington, USA, ensuring that assets were inspected and service was maintained without putting any of their workers in danger.
Here’s what autonomous site inspections mean for telecommunications companies:
- Faster and better responses to both routine and emergency needs.
- Consistent and persistent visual inspections enable smart decisions based on data to boost productivity and efficiency.
- Visual, thermal and radiometric inspection capabilities make it easy to optimize maintenance.
- Immediate alerts to safety hazards minimize safety risks.
- Enhanced security with regular perimeter and area patrols.
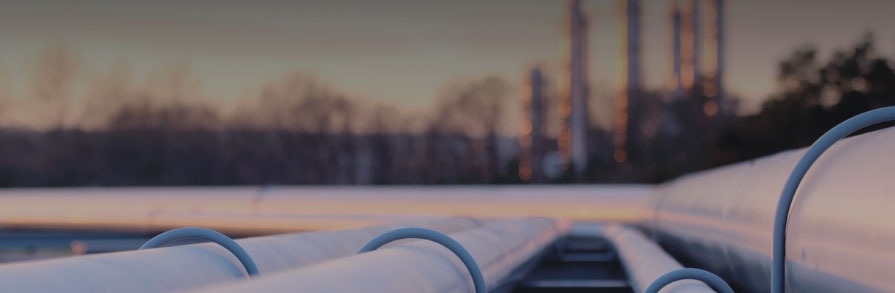
Other industrial sites
All heavy industry sites seek the balance between maximizing production while still ensuring site safety, security and regulatory compliance. To strike this balance effectively, site managers must have a clear picture of all operational details. This is a challenge when sites are large and spread out and there is no central repository for collecting data gathered from site inspections whenever they do occur. At ICL Dead Sea, for example, autonomous inspections enable crews to monitor and secure the chemical site in the most efficient and safe way possible.
Here’s what autonomous site inspections mean for heavy industry sites:
- Routine perimeter patrols ensure site security, even in the most remote locations.
- Thermal mapping monitors temperature sensitive locations for anomalies.
- Personnel are automatically alerted to safety risks.
- Immediate situational awareness in the event of an emergency for a quicker and safer response.
- Routine inspections are made possible, even for hard-to-access assets.
- Consistent monitoring and archiving of site conditions will ensure and prove compliance with all regulations.
What companies have already implemented autonomous inspection solutions?
Companies around the world have begun integrating autonomous drones and robots into their daily operations to fully automate key inspections and monitoring. Here are a few examples of how companies in different industries are benefiting from this technology.
Verizon
Among the disasters of 2020 was the Big Hollow Fire in Washington State that burned over 24,000 acres and resulted in the evacuation of thousands of people. As one of the communications providers in the area, Verizon had to inspect their infrastructure to make sure that their customers, and more importantly, first responders, would be able to communicate.
Verizon was able to get a special emergency waiver from the FAA to allow them to fly Percepto’s drones beyond the visual line of sight (BVLOS) giving Verizon employees the ability to operate the drones from the safety of their own homes and no human pilot on site, with one employee watching the inspection from as far as Alaska.
Autonomous inspections in this situation is a gamechanger. There is no longer a need to risk human life to inspect infrastructure and get it back in working order during natural disasters.
Florida Power & Light
Florida Power & Light (FPL) provides electricity to over 9 million customers in Florida. As a state that is pummeled by hurricanes every year, the company is committed to providing continuous power to residents and trying to reduce the costs of damages, which can be in the billions of dollars.
FPL has been using Percepto to remotely identify power failures after a storm, ensuring that they can be fixed quickly without risking sending employees in to perform inspections. The Percepto Base can withstand hurricane 5 level winds, making it the only solution that can respond to hurricane damage immediately. The drones also have both day and night camera systems so that images can be captured regardless of the time of day that a storm hits. Personnel receive alerts on malfunctions and safety risks detected by AI-powered change detection algorithms. All relevant stakeholders are able to request and access the data they need to gain valuable insights as to the health of their assets.
Delek US
Delek US is a US downstream energy company that was looking for ways to reduce their environmental footprint,improve employee safety and improve their bottom line at one of their refineries. These tend to be conflicting goals and it was a challenge to meet them all at once.
With the installation of Percepto’s solution, the refinery was able to automate a number of tasks that otherwise required significant time and resources, thus maximizing productivity. Specifically, they began using Percepto’s drones for their emergency response program, which gave them better visibility leading to better decision-making and better safety. In addition, Percepto’s solution meant that Delek personnel did not need to climb high towers, go inside vessels, check on floating roofs in the tank farm or observe pipeline routes in order to gather and analyze data needed to run operations smoothly.
Enel
One of Europe’s largest energy companies, Enel was one of the first to implement autonomous drone technology. Enel’s operations and security managers wanted to acquire meaningful insights that would help optimize production while reducing maintenance costs and response times. They felt that existing drone solutions that required pilots had limited value due to availability constraints. And, the technologies were not able to capture the constant data streams required to really obtain actionable insights rather than sporadic snippets that leave a lot to guesswork.
Percepto’s solution provided Enel’s Civitavecchia power plant with 24/7 data collection giving them the real-time information they needed without being dependent on pilots and support teams. They used the system to support the operation, maintenance and protection of the plant. The system also improved the plant’s overall environmental performance, as well as increased its efficiency. Using this system, Enel reduced the risk to their employees and reduced maintenance costs while also improving their decision making and ability to respond to events immediately.
RockBlast
RockBlast is the go-to company for technological innovation in Chile’s mining sector. The company provides engineering services to the mining industry with a focus on innovation in drilling and blasting, geomechanics and technological developments. Because mining operations are geographically remote, and extremely risky, an autonomous inspection system is especially valuable. RockBlast offers its clients access to Percepto’s autonomous drones for automating tasks such as pile inspections and aerial surveys for blast site planning. By implementing this system, RockBlast’s clients experience better site safety and productivity, stricter compliance with regulations and improved security.
Large mining facility in Australia
A large mining conglomerate in Australia is one of the first to embrace the remote operations trend that is going to continue to grow in popularity. As one of the only mining companies in the world with a large remote operations center from which they manage all of their facilities, the company added Percepto drones to their fleet of autonomous trucks and other automated solutions. For the first time ever, the remote operations offered by Percepto allows them to inspect and monitor their facilities worldwide on a day-to-day basis.
Specifically, this company uses Percepto’s solution for 3D mapping, pile inspection and volumetric measurements and ongoing site inspections. As mines are well known for their safety risks, the company was thrilled with the ability to send in a robot instead of a person, significantly reducing the risk to employees.
ICL Dead Sea
Israel Chemical Industries (ICL) Dead Sea is an innovative potash facility operating on its privately owned power grid, leaving it particularly vulnerable to potential points of failure and unplanned downtime. Manual inspections were very costly and time consuming and in some cases required shutting down the infrastructure.
ICL Dead Sea began using Percepto’s system to collect high-quality data and receive actionable insights in the following areas: power grid inspection to identify faults with AI-powered anomaly detection; 24/7 thermal inspections that provide immediate notification of failures; 3D pile inspections to support logistics team and materials transportation; pipe inspections; security patrols; and emergency response to any fires or leaks.
With constant monitoring and reporting, ICL Dead Sea’s site managers are always fully aware of everything happening all across the site. They can decrease downtime while boosting safety and efficiency, all at a fraction of the time and cost of manual inspections.
FAQs when considering an autonomous inspection and monitoring solution
Working with leading energy, oil & gas, mining and telecommunications companies around the world, we get a lot of questions about autonomous inspections, especially the challenges involved. Here, we will share some of those questions and their answers.
Are there a lot of regulations involved with flying drones?
The current buzzword in drone regulations is BVLOS (Beyond Visual Line of Site). BVLOS operations basically mean operating a drone without an operator on site looking at the drone and deconflicting the airspace. Most world regulators don’t allow drones to operate BVLOS without special approvals, and many companies don’t want to have an employee on site to monitor drones. Percepto has received regulatory approval and BVLOS waivers in several countries. In addition, Percepto is also one of the top 10 companies in the process of being Type Certified (TC) by the FAA, running for the FAA’s type certificate (TC), which will streamline BVLOS approvals in the US for any certified solution.
Do autonomous inspection systems flag a lot of false alarms?
What about privacy concerns? Are the drones watching employees?
What happens to drones and robots in bad weather?
Are autonomous site inspections expensive?
Is it worth investing in this new technology - is it field proven?
Will this technology eliminate jobs?
Over to you
If you made it to the end, congratulations – you are now an autonomous inspection and monitoring expert. If you still have any questions that we didn’t cover here, or want to dive a little deeper into a specific topic or use case, you can reach out to a fellow AIM expert anytime.